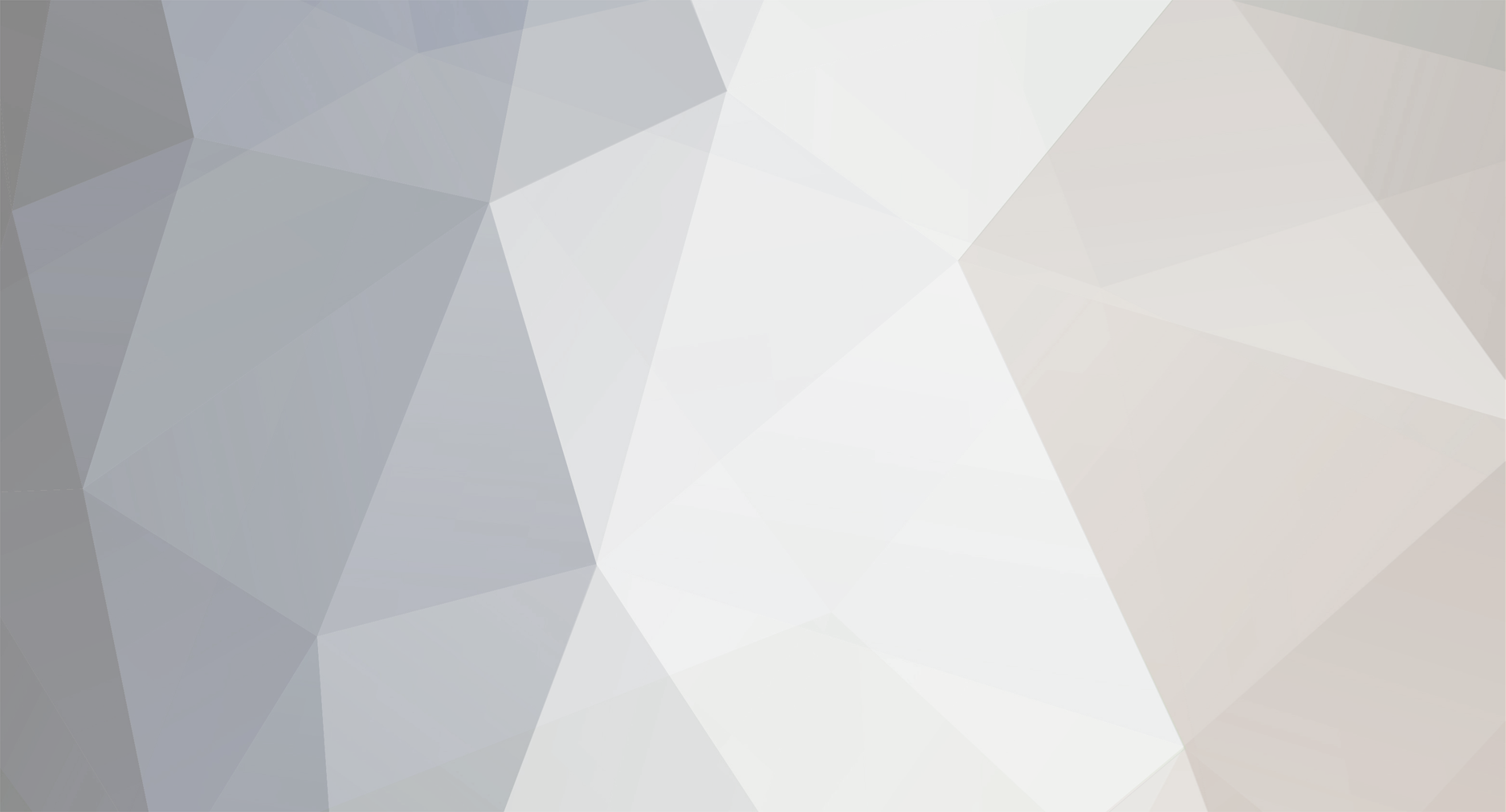
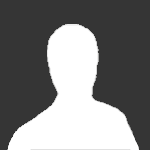
Shakemsam
Members-
Posts
678 -
Joined
-
Last visited
Content Type
Profiles
Forums
Events
Gallery
Store
Everything posted by Shakemsam
-
The adding a link to the breakaway cable...bad idea. The length of that cable is key to when the brakes react. Adding a link delays that reaction. Don't do it! Now, as I mentioned previously.. The metal clip on the breakaway cable is designed to be inside the actuator. When the cable is pulled with force (usually when you pull away and forget to disconnect it), the brakes are activated and the clip keeps the cable extended, keeping the brakes from releasing. Now the cable is similar to your emergency break cable in your car but different because it does not go all the way to your wheels. The cable is generally attached to a lever on the actuator that when pulled, activates the brakes. Most actuators are mounted above the tongue and all the above would be in plain view. Eagle integrated it into the tongue for appearance. You will have to remove the actuator to service it. That S hook is tempered steel. It is tough for a reason. If it was easy to bend, it wouldn't serve it's purpose very well. Like a previous poster suggested...try some heat! If the trailer moves without issue, then the brakes simply are not working. Considering that you didn't know you had brakes...I am sure that the actuator is dry if not full of water. Remove the black cap behind the coupler. That's where the brake fluid goes. Reg DOT fluid is fine. Now, at the wheels...you could have disc or drum brakes. Servicing the brakes can be a chore. Disc are the easier of the two. Either way, the wheels will have to be removed. If it is drum brakes, the hubs have to come off. If disc, they resemble automotive disc brakes and are self explanatory. My guess...you will have drum brakes and the wheel cylinders are frozen. Replace the cylinders, maybe the shoes, and some hardware. With any luck, the actuator isn't froze but not likely. Rebuild kits are available but I generally just replace the whole thing. If the hoses and lines appear ok, next is bleeding the brakes and adjusting the shoes to the hubs. Sounds like a lot and it is, but it's not terrible. It's also a PITA with the boat on but it can be done. Good Luck and PM me if you have any ?
-
Yep! That looks like either a Tiedown or Dexter actuator. Alumacrafts are generally packaged with Eagle trailers. If that trailer doesn't have brakes, it did at one time! And if it does...they ain't workin! BTW, that metal clip on the cable should be inside the coupler. Being outside means the emergency brake is activated.
-
what about installing a hatch and use the area for storage.
-
If the transom is all good and no other work is required, go to the lumber yard and get yourself some round hardwood stock just bigger than the holes. Drilling the holes to accommodate the size of stock might be required. Cut them so they will be flush to the outside skins. Coat them with 5200 and drive them in. Sand and paint.
-
I keep a ratchet on it except for when it's running.
-
Just once or constantly? Every Merc I've owned..clicked going into gear. It is quite loud when done out of the water..
-
Have you tried shifting it while running?
-
-
Sold / Closed 115 & 8 hp Johnson outboard pair SOLD
Shakemsam replied to scobar's topic in Classifieds - Buy, Sell, Trade or Rent
-
Are you referring to the Vhf's power cord plug? If so, I can't imagine that it would.
-
for sale : usa J-Plugs and misc spoons (SOLD)
Shakemsam replied to Shakemsam's topic in Classifieds - Buy, Sell, Trade or Rent
-
for sale : usa Misc Bass cranks (SOLD)
Shakemsam replied to Shakemsam's topic in Classifieds - Buy, Sell, Trade or Rent
-
for sale : usa Misc Sticks (SOLD)
Shakemsam replied to Shakemsam's topic in Classifieds - Buy, Sell, Trade or Rent
-
for sale : usa Misc Jointed Sticks
Shakemsam replied to Shakemsam's topic in Classifieds - Buy, Sell, Trade or Rent
-
for sale : usa Penn Rival 20LW NIB $45 shipped
Shakemsam replied to Shakemsam's topic in Classifieds - Buy, Sell, Trade or Rent
-
-
-
-
Be sure to re-use the inserts for the transom holes or replace with new. Coat them liberally with 5200. Keep their location in mind if you are putting the kicker directly on the transom vs a bracket. If transom, mount a piece of starboard inside the splashwell so the pressure from the kicker mount is spread out. In lew of starboard, I use black poly cutting board that I buy at Walmart. I also use it for transducer plates. Cuts easy and routs nice too and lots cheaper.
-
Nice Rig! Running a 90 195 Sportfisherman that I picked up a few years ago. I would imagine the transom wasn't through bolted to due the lack of access without removing all the foam. The only through bolts I have access to are the motor bolts. Keep in mind that aluminum and stainless don't mix well, just like aluminum and PT wood. Unfortunately not really any other options though. Having a good painted surface on the aluminum helps. You can also add a plastic washer as a barrier between the hull and any stainless nut, bolt head, or washer. I like your use of the Lowrance for gauges but I would be concerned with the chance of a network failure. I would have a voltmeter at a min and maybe engine temp. Good Luck!
-
Alpha... if it was me.
-
for sale : usa Penn Rival 20LW NIB $45 shipped
Shakemsam posted a topic in Classifieds - Buy, Sell, Trade or Rent
-
for sale : usa Misc Jointed Sticks
Shakemsam posted a topic in Classifieds - Buy, Sell, Trade or Rent
-
for sale : usa Misc Sticks (SOLD)
Shakemsam posted a topic in Classifieds - Buy, Sell, Trade or Rent
-
for sale : usa Misc Bass cranks (SOLD)
Shakemsam posted a topic in Classifieds - Buy, Sell, Trade or Rent